From a large steel sheet to a finished product, each stamping part goes through several processes: blanking, stamping, piercing, welding, surface treatment, and more.
Many factors affect the blanking process, such as the size, shape, and raw material of the part, as well as the steel sheet, machines, layout, and molds used.
1. Check the steel sheet before blanking
After shearing, there may be some incomplete edge sheets. Therefore, it is necessary to check the completeness of the sheets before starting the blanking process.
2. Choose the appropriate stamping machine
Different parts have different sizes and material thicknesses, which require stamping machines with different tonnages.
3. Optimize the layout
To control product costs, it is important to maximize the utilization of raw materials.
Raw material utilization rate = Part weight / Raw material weight
The closer the rate is to 1, the better. Therefore, it is recommended to blank as many parts as possible from a single steel sheet.
To achieve a better utilization rate, please refer to the following layouts:
3-1 The material usage rate varies depending on the arrangement of parts on the material, such as straight, diagonal, opposite, multi-row, and edge-blanking.
Picture 1: The first layout scheme is designed for single-sided rows only, resulting in more scrap and a material usage rate of only 53%.
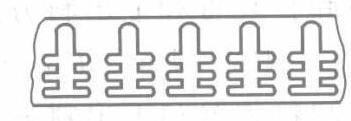
Picture 2: The second solution utilizes staggered rows on both sides to optimize the limited material space, resulting in a material usage rate of 68.5%.
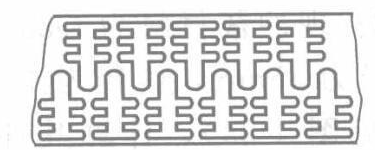
3-2 From a waste perspective, there are three types: with waste, with less waste, and without waste.
When there is a scrap arrangement, there are lap edges between workpieces and between workpieces and the strip. This ensures the quality of the punched parts and protects the die, but the material utilization rate is low. When there is less or no scrap arrangement, there are fewer or no lap edges, resulting in a higher material utilization rate. However, the die may be easily damaged due to uneven lateral forces during punching.
Using less or no scrap arrangement is significant in reducing the cost of stamping parts and improving production efficiency by allowing the stamping of multiple products simultaneously. Additionally, it simplifies the structure of medium-pressure dies and reduces punching force. The material utilization rate can reach 95% for scrap-free patterns and 70%-90% for patterns with less scrap.
3-3 Nesting of different products involves using the scrap from product A to stamp out the shape of product B. This requires careful coordination and batch operation. In my more than 7 years of experience in hardware work, I have encountered such cases twice, resulting in nearly half the cost savings for product B.
Of course, improving material utilization is not the only consideration. The layout of samples also affects the accuracy of punched parts, productivity, die life, economic efficiency, and other factors. It is important to consider production convenience, workshop conditions, and the reasonable structure of the die. In other words, it is necessary to weigh the advantages and disadvantages from all aspects and choose a layout plan that is suitable for your stamping plant.
4. Mold design
The design of single molds and progressive molds differ in terms of time efficiency and material utilization.
Blanking may seem simple, but as the first step in many processes, it significantly impacts the subsequent steps. It is crucial to ensure that every step is carried out correctly.
Different parts have different sizes and material thicknesses, which require stamping machines with different tonnages.